摘 要:喷油泵凸轮轴和滚轮传动部件的检修是喷油泵检修中的重要部分,文章讲述了凸轮轴和滚轮损伤的原因,以及从凸轮轴的轴向间隙、凸轮工作表面磨损、凸轮轴弯曲和滚轮架总成四方面具体讲述了检查、调整、修理。
喷油泵凸轮轴和滚轮传动部件的检修是喷油泵检修中一个较为重要的部分,凸轮和滚轮传动部件在泵中发挥着不可替代的作用。凸轮轴的凸轮与滚轮接触处会受到磨损,严重时将形成沟槽,使其供油规律发生变化。凸轮轴两端的滚珠轴承磨损时,使凸轮轴的轴向间隙增大,在喷油泵运转中会发生响声。凸轮轴与轴套间隙增大至0.15mm,会导致调速器工作不正常,严重时还会影响柴油机的工作性能。
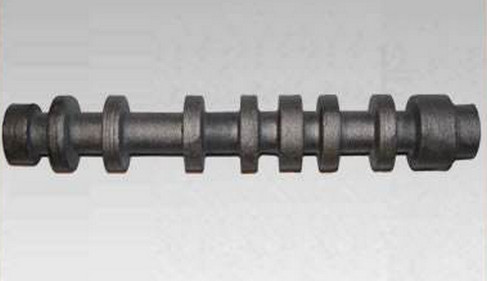
一、凸轮轴和滚轮损伤的原因
凸轮轴和滚轮是一对摩擦副,其间还承受周期性的冲击载荷,因此,它们需具有足够的韧性和刚度,能承受冲击载荷。这类摩擦副的摩擦表面上常见的有磨损、擦伤和麻点三种。磨损包括缓慢的抛光过程而形成的一个硬而光滑的摩擦面和随时间延长而产生的正常磨损。擦伤是一种严重的表面损坏,它是在较高的表面接触压力下,由于润滑不良引起干或半干摩擦造成的金属熔着,并能迅速发展成相互咬住。麻点是摩擦表面在交变压力载荷下,于材料的缺陷处产生裂痕,扩展而形成表面材料剥落。凸轮轴和滚轮损伤的原因:
1.润滑不良。有的是因为缺油运行;有的是因为润滑油中混入过量柴油造成润滑性能下降;有的是因为润滑油中含水造成锈蚀。
2.柱塞弹簧折断有可能形成弹簧碎圈重叠,从而造成凸轮上升段受力剧增,迅速磨损。
3.凸轮与滚轮的接触,在理论上讲是线接触,实际上由于材料弹性变形而成小矩形的面接触。但在实际使用中,滚轮传动部件因其定位螺钉松动而偏转,致使滚轮偏离凸轮滚道,使得滚轮端面棱角与凸轮表面接触,从而使凸轮表面产生严重的划伤和磨损。
二、凸轮轴和滚轮传动部件的检修
1.凸轮轴轴向间隙的检查与调整
大多数发动机的凸轮轴采用止推凸缘定位,其轴向间隙的检查方法是:将止推凸缘尽量推向齿轮或链轮一侧,用塞尺插入止推凸缘和凸轮轴颈的侧面,测得的间隙值即为轴向间隙值。一般发动机凸轮轴轴向间隙值为0.05~0.20mm,*大应不超过0.25mm。凸轮轴轴向间隙是以止推凸缘与隔圈的厚度差来决定的,当止推凸缘磨损变薄使间隙过大时,可更换加厚止推凸缘以恢复正常间隙;若间隙过小,可减薄止推凸缘,也可在凸轮轴前端台肩上加垫。
2.凸轮工作表面磨损的修理
在使用过程中,滚轮与凸轮磨损,柱塞末端与垫块长期的频繁冲击,垫块平面被冲成半圆形凹坑,磨损后的重迭高度下降,致使供油落后,发动机着火困难,功率下降,且因四缸磨损不一,四缸供油时间误差增大,发动机工作不平稳。凸轮工作表面磨损后的修理:
(1)表面有较轻微划痕和磨损,可给予修磨。凸轮的升程和回程工作面磨损不同,因此原设计的凸轮轴允许调头使用,以延长使用时间。调头使用时只工作顺序改变,所以在发动机上安装时,应将二、三缸油管对调即可。
(2)当凸轮工作面局部磨损不超过0.3mm时,可在凸轮轴磨床上磨削,消除磨损痕迹,恢复凸轮的正确几何形状。
(3)当磨损已超过0.3mm时,则可用堆焊法修复。将凸轮轴用专用夹具固定,置于水中露出待焊部位,用中碳钢焊条进行堆焊,然后按标准尺寸磨出正确几何形状。
(4)键槽磨损可采用修理尺寸法,将键槽铣宽到5~6mm,配以相应的键。也可采用堆焊后重新开键槽的方法来修复。
3.凸轮轴弯曲的检查与修理
凸轮轴弯曲使套装在凸轮轴前端的圆锥滚子轴承所受的作用力*大,使轴承座圈“走外圆”、轴承盖松动和外移、凸轮轴窜动量增加,凸轮、挺杆钢球、齿轮箱中互相啮合的正时齿轮的磨损加速,严重时,还可导致轴承滚柱支持架碎裂、泵内润滑油从松动的轴承盖边缘泄漏、正时齿轮崩裂等。检查凸轮轴弯曲变形,可用其两端轴颈外圆或两端的中心孔作基准,测量中间一道轴颈的径向圆跳动量。凸轮径向圆跳动量一般为0.01~0.03mm,允许极限一般为0.05~0.10mm。若超过极限值,可对凸轮轴进行冷压校正,必要时应更换。
4.滚轮架总成检修
滚轮架磨损严重时,可以看到一道道很深的划痕。这是由于润滑油中机械杂质进入滚轮架与泵体孔配合间隙擦伤的结果。滚轮架与座孔的配合间隙应为0.02~0.10mm。超过规定时,对其采取镀铬磨光法修理,其表面粗糙度Ra<0.4Rm。泵体座孔采取铿削法修理,加工时必须使用专用卡具,以防止座孔中心线偏移,其表面粗糙度Ra<0.8μm。座孔镬削尺寸需要根据光磨后的滚轮架尺寸配镗,使其配合间隙恢复到原有标准。有些喷油泵泵体座孔可采取镗大镶套的方法修理,其技术要求同上。
滚轮轴的松旷也往往将滚轮架上的轴孔磨成椭圆形。由于配合间隙过大,在运转中还会发生异响。该配合间隙不得超过0.05mm,超过时应更换新的滚轮轴。
检查滚轮轴与滚轮衬套之间和滚轮衬套与滚轮之间配合的总间隙,其值应为0.02~0.25mm。否则,允许用选配滚轮衬套的方法恢复标准配合间隙。